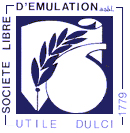
Agenda
Activités
Bulletin
d'Information
Publications
Historique
Contacts
Liens
|
|
Société
libre d'Emulation - Liège
(Belgique)
Visite
guidée
20 février 2004
La
ligne à chaud de
Cockerill-Sambre
La sidérurgie à chaud du bassin
liégeois de Cockerill-Sambre a fait la " une " des
journaux au début de l'année 2003 lorsque la
maison-mère ARCELOR &endash; holding formé de
la fusion du luxembourgeois ARBED, du français USINOR
(déjà propriétaire de Cockerill-Sambre)
et de l'espagnol ENSIDESA (Avilès) - a annoncé
sa décision, pour raisons de rentabilité, de
fermer ses sites de production " continentaux " au profit de
ses sites " maritimes " : Brême, Gand, Dunkerque,
Avilès et Fos. Après de longues palabres
syndicales et politiques, il a été admis que
la production serait dans un premier temps, au 1/1/2005,
réduite de moitié par l'arrêt d'un
haut-fourneau à Seraing et totalement en 2009 par
l'arrêt du deuxième Haut-Fourneau à
Ougrée et de l'aciérie et du train à
chaud de Chertal.
Il nous a semblé opportun, à la veille de
la fermeture d'un outil qui fit la réputation de
Liège, d'aller lui rendre une dernière visite.
En fait, nous ne visiterons que la partie avale du
processus. En effet, l'aciérie de Chertal est
alimentée en " fonte " à partir des
hauts-fourneaux d'Ougrée et de Seraing, au moyen des
longs convois de " wagons-thermos " que l'on voit circuler
sur les voies de chemin de fer de Liège-Est :
Kinkempois, Angleur, Vennes, Longdoz, Jupille, Wandre, Ile
Monsin
Dans les hauts-fourneaux, le minerai de fer est "
réduit " par le " coke " et donne un métal
liquide, la "fonte ", composé essentiellement de fer
et de carbone (± 4.5 %). A la température de
1500°C, cette " fonte " est transvasée dans ces
wagons-thermos d'une capacité de quelque 150 tonnes.
Arrivée à l'aciérie de Chertal, cette "
fonte " liquide est transformée en acier dans des "
convertisseurs ", où le carbone est
brûlé par de l'oxygène. Cet acier
liquide à la température de 1650 °C est
ensuite transvasé dans des poches de 200 tonnes de
capacité, traité pour être mis à
nuance, et ensuite " coulé " dans une machine de
coulée continue où il est solidifié
sous forme d'un ruban d'acier de largeur variable (1
à 2 m) et de 250 mm d'épaisseur,
débité à longueur en " brames " de 10
à 12 m de long, en fin de ligne.
Ces " brames " sont ensuite ± refroidies puis
réchauffées à bonne température
pour être lami-nées en tôles de ± 5
mm d'épaisseur et " bobinées " en bobines de
±1200 kg. Ces bobines sont à leur tour
chargées sur des wagons et acheminées vers
Renory. Elles seront la matière première pour
" la ligne à froid " (Tilleur et Jemeppe) : laminage
à froid en fines épaisseurs, recuits puis
étamage ou galvanisation suivant la destination.
C'est la partie coulée continue et train à
larges bandes que nous visiterons.
Guy Dehalu
Rendez-vous à 14 heures 15 au poste de garde à
l'entrée de l'usine de Chertal.
PAF : 5 Euros - 4 Euros (membres de l'Emulation) - 2,50
Euros étudiants de moins de 26 ans
|